.png)
The solid substrate material (the catalytic material upon which chemical species react) in the fluidized bed reactor is typically supported by a porous plate, known as a distributor. The fluid is then forced through the distributor up through the solid material. At lower fluid velocities, the solids remain in place as the fluid passes through the voids in the material. This is known as a packed bed reactor. As the fluid velocity is increased, the reactor will reach a stage where the force of the fluid on the solids is enough to balance the weight of the solid material. This stage is known as incipient fluidization and occurs at this minimum fluidization velocity. Once this minimum velocity is surpassed, the contents of the reactor bed begin to expand and swirl around much like an agitated tank or boiling pot of water. The reactor is now a fluidized bed. Depending on the operating conditions and properties of the solid phase various flow regimes can be observed in this reactor.
- High sludge retention time, short retention time, and small reactor size
- The active carbon can absorb toxic compounds and shock loads
- High quality of the effluent (low total suspended solids (tss) and chemical oxygen demand (cod))
- If oxygen is supplied to the reactor, the emission of toxic compounds into the atmosphere is avoided.
- The mechanisms are not fully understood and therefore the technology needs to be tested on a pilot plant scale.
- For very small or low-density carrier media, the solid hold-up decreases rapidly and particle elutriation becomes severe as the gas flow rate is increased.
- The increased agitation in the FBR caused by the gas bubble motion can result in the shedding of the attached biofilm
- The exhaustive control of the gas and liquid flow is required to maintain adequate bed expansion and gas-liquid transfer while minimizing shear effects and particle elutriation

Fluidized-bed reactors are theoretically an excellent choice for highly exothermic reactions, such as the FT reaction. Compared with fixed-bed reactors, fluidized-bed reactors offer much higher efficiency in heat exchange and better temperature control due to the turbulent gas flow and rapid circulation (Ouadi et al., 2019b).
These reactors operate at high pressure and temperature, leading to enhanced efficiency and providing superior heat transfer, enhanced temperature control on highly exothermic FT reactions, and simple catalyst handling (Motta et al., 2018).
Get A Free Quote For Manufacturing & Fabricating
Contact us at the Industrial nearest to you or submit a business inquiry online.
Contact Us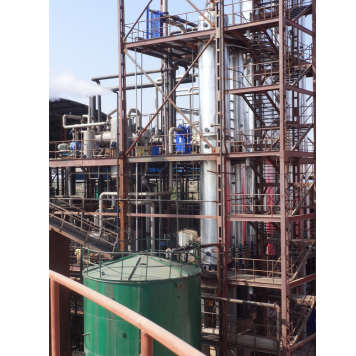
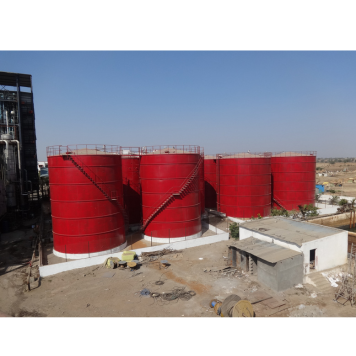